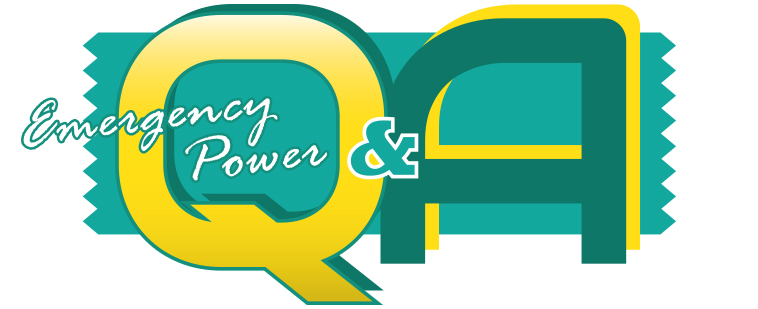
Many questions arise when beginning your first emergency power connection equipment project. ESL has put together some Frequently Asked Questions from customers throughout the years to assist as you move forward with choosing your back up power solution.
General
Q: How do I know what product will best work with my specific needs?
A: ESL’s knowledgeable sales personnel will gladly assist with helping to identify the proper product for your application. The key factors will be the voltage system and the desired emergency load that is to be fed.
Q: What is UL 1008 and how does it affect me?
A: Local building inspectors typically require all new electrical equipment installed in their jurisdiction to be “Listed” which means the equipment has been approved by Underwriter Laboratories or another recognized test lab. For standby systems that allow portable generator connection, UL 1008 is the proper standard to comply to. If the equipment is not Listed, it may not be acceptable to the inspector.
Q: Is it difficult to make the generator connection to the StormSwitch®, TripleSwitch® or TempTap® product line?
A: No, they utilize the industry standard 400A series 16 cam-style connectors. ESL’s StormSwitch, TripleSwitch and TempTap are color-coded to the voltage, e.g. 208Y/120 green, white, black, red, blue.
Q: Do the generators have the same color-coded plugs that the StormSwitch, TempTap, and TripleSwitch have?
A: ESL cannot guarantee that. Industry standard is green for ground, white for neutral, and typically black for “A” phase, red for “B” phase and blue for “C” phase. When entering in an agreement for generator service, it is recommended that you request the aforementioned color-coding for the cams.
StormSwitch
Q: What are the advantages/disadvantages of using a manual transfer switch with a portable generator versus an automatic transfer switch with a permanent generator?
A: Advantages:
Significantly lower cost
No on-site fuel storage required
No maintenance or standard periodic testing
Easier installation – days instead of weeks
Smaller size
Portable generator can be rented or used at other facilities
Permanent generator requires multiple permits
Disadvantages:
Longer time before generator power is established
Q: Can the StormSwitch be Service Entrance Rated?
A: Yes, the StormSwitch has the option to be SUSE (Suitable for Use as Service Entrance in the USA). This option should only be used when the StormSwitch is installed at the building service entrance.
Q: What is the reason an additional circuit breaker is available with the purchase of a StormSwitch?
A: Circuit breakers provide over current protection; switches do not. If the supplied generator does not have built in over current protection, then it is recommended that the generator disconnect and the StormSwitch be equipped with a circuit breaker rather than a switch. Also depending on your specific application, you may or may not need over current protection on the utility side. Again, ESL’s knowledgeable Sales personnel will gladly help you in deciding what combination works best for your application.
Q: How does the StormSwitch compare to a standard “double-throw” or “double-key” transfer box?
A: The traditional “safety switch” and/or “double-throw” switches do not provide the over current protection option that is available in ESL’s StormSwitch. These “safety switch” and/or “double-throw” switches are intended for “hard wiring” and therefore would require a licensed electrician (difficult to find one available as they are in high demand during power outages) to connect and disconnect the generator.
Additional StormSwitch Q&A can be found here
TempTap
Q: What is a TempTap?
A; Also referred to as a docking station or tap box, ESL’s TempTap is a means for direct connection from the generator to the building’s switchgear.
Q: Is there any protection offered in a TempTap?
A: Locking doors and internal connection points to keep unauthorized persons from the device. The TempTap is designed to be a safe and simple pass-through box mounted to the outside of a building. It should be used in conjunction with a with a transfer switch or a utility disconnect.
TripleSwitch
Q: What is the TripleSwitch designed to do?
A: The UL 1008 Listed TripleSwitch was designed to simplify and reduce the cost of load bank testing procedures and to provide a backup for the permanent generator. This unique 3-way manual transfer switch system provides a quick and completely safe way with mechanically interlocked breakers to supply power to the facility from a portable emergency standby generator in the event the utility power is disrupted due to a power loss when the permanent generators are offline.
Q: I know it’s easy to show the ease of use and the safety aspects of the TripleSwitch, but are there other advantages as well?
A: Yes, an added benefit is a reduction in down time when connecting and disconnecting for load bank testing. Having quick connect cam locks for connecting the portable load bank means set up time is reduced to minutes not hours.
Q: How difficult is this to install a TripleSwitch on a job site?
A: Being UL1008 Listed means the TripleSwitch is built in an enclosure designed to provide the proper bend radius and space for the cable amperage being used. The TripleSwitch is an integrated unit with all necessary breakers and cam-lock connections. This means the contractor is installing one unit thus reducing conduit runs and cable lengths as opposed to alternative multiple unit and switchgear solutions that would require multiple conduit runs.
Q: Can I install the TripleSwitch with an existing permanent generator?
A: Yes, very easily. Being an integrated unit, you typically do not need to design-in new breakers and interlock methods. It is a drop-in solution connecting into the existing connection between the ATS and permanent generator.
ESL’s knowledgeable sales personnel is here to answer any additional questions you may have. Please feel free to contact us! ESL is always here to help!